2.
APPLICATIONS OF UNMANNED AIRCRAFT SYSTEMS IN AGRICULTURE
To enhance agricultural intensity, automation, robotics, information services, artificial intelligence (AI), big data, and the Internet of Things are essential. Smart agriculture is an evolving field that creates new opportunities for the future. At the core of smart agriculture development are agricultural robots, including unmanned aircraft systems (UAS). The use of UAS has contributed to the expansion of various agricultural sectors, including scouting and foliar fertilization, aerial seeding, and weed (pest) detection, while also driving advancements in field mapping and yield forecasting.
Drones are effectively utilized in both major branches of agriculture: crop production and livestock farming. In crop production, the primary goal of UAS application is to preserve yields, while in livestock farming, it focuses on reducing management costs, ensuring herd safety, and monitoring feed resources. The specific applications of drones in crop production and livestock farming are presented in Tables 2.1, 2.2, and 2.3.
Arguments on the Advantages of UAS Over Manned Aircraft
Unmanned aircraft systems (UAS) have significant cost advantages over manned aviation. For example, the price of an agricultural aircraft such as the Single Squirrel AS350 is €3.6 million, with a payload capacity of 600 kg, a 10-meter spray boom, operating parameters of approximately 40 m/s at an altitude of 30 meters, and a spray amplitude of 50 meters. Its operational efficiency is 80 hectares per flight, with each flight lasting 25 minutes. The aircraft requires two pilots for operation and an additional four specialists for ground maintenance.
In contrast, the cost of an agricultural drone, such as the DJI Agras T30, does not exceed €25,000, making it an affordable option even for small farms. When comparing the theoretical maximum efficiency in terms of cost per hectare, the total lifecycle cost for the aircraft appears attractive, at approximately 450 RUB per hectare (excluding airworthiness maintenance expenses). However, when factoring in aircraft downtime due to excess capacity, this cost rises to 800 RUB per hectare or more, making the economic efficiency of a drone as a substitute for an aircraft in small to mid-sized farms more apparent. A drone can operate at approximately 500 RUB per hectare, assuming an annual workload of 10,000 hectares in spraying mode with an application rate of 10 liters per hectare.
Additionally, the maintenance and repair of agricultural drones are relatively simple. Operators can replace propellers and nozzles, while more complex repairs, such as replacing motors with speed controllers, arms, or landing gear, can be quickly performed by trained personnel.
The Use of UAS in Crop Production and the Concept of Precision Agriculture
The use of unmanned aerial systems (UAS) in crop production is developing alongside the concept of precision agriculture. Precision agriculture is a management approach based on the understanding that a field is not homogeneous and that its variability can and should be taken into account when performing agricultural operations. The concept—or system—of precision agricultural management is based on the integration of centimeter-accurate navigation technologies, yield monitoring technologies (YMT), geographic information systems (GIS), remote sensing (RS), variable rate technology (VRT), 3D modeling, digital twins, and more.
This approach to agriculture takes into account the differentiated conditions within a single field, which leads to increased efficiency and resource savings in agricultural production.
Although purchasing a drone is significantly less expensive than buying an airplane or an agricultural sprayer, the rise in popularity of drones—and agricultural drones in particular—is driven largely by factors other than cost. As an analogy, consider the use of mobile (cellular) communication. Mobile phone plans are typically more expensive than landline services, yet this did not prevent the widespread shift to mobile communication for daily use. Humanity has come to value the risk of delayed information more than the extra cost of mobile connectivity compared to landline services.
In crop production, for a specific farmer, an agricultural drone and/or a small monitoring drone functions much like a mobile phone—enabling independent, timely treatment or data collection at any moment, without wondering whether a requested airplane/helicopter/ultralight aircraft will show up, without waiting for a tractor to access a field after rain, and without depending on delayed satellite imagery updates in an app to obtain survey results.
Table 2.4 presents models of the most common types of agricultural UAS, categorized by areas of application.
2.1
OBSERVATION, MONITORING, AND INSPECTION
TWO TYPES OF UAS FOR FIELD OBSERVATION
Two types of unmanned aerial systems (UAS) are used for field observation, differing in design and flight characteristics:
1. Fixed-Wing (Flying Wing) UAS – This is the most suitable option for surveying large areas due to its superior aerodynamics. Fixed-wing UAS are best suited for monitoring extensive areas or conducting aerial photography over long distances. However, due to their design, they must remain in continuous motion, making them incapable of hovering over a specific area or conducting localized surveys in confined spaces.
2. Multirotor (Copter) UAS – These drones can be equipped with varying numbers of rotors, making them ideal for precise imaging in a fixed location, surveying small land plots, and generating 3D models. Multirotor UAS are characterized by their simple design, flight stability, and reliability. However, they have lower speeds and shorter flight durations, which limits their operational range compared to fixed-wing UAS.
EXAMPLES OF UAS APPLICATIONS:
• Routine diagnostics: Aerial inspections of power lines, low- and mid-altitude photography, security zone monitoring, defect and violation detection, and spatial (3D) analysis of clearances and wires.
• Data collection for emergency restoration work.
• Cartographic work: Creation of digital topographic and cadastral maps, 3D terrain and object modeling, and support for construction and reconstruction projects.
• Assessment of crop emergence.
• Evaluation of nitrogen nutrition levels in plants.
• Monitoring the phytosanitary condition of crops.
The use of UAS significantly enhances the efficiency of monitoring and reduces the time required for inspections, maintenance, and repair work.
UAS for data collection (imaging) are widely used in various industries, including ecology and environmental management, geodesy, cartography, mining, and, of course, agriculture.
Figure 2.1 presents an example of aerial imagery captured by both satellite and drone. The analysis of the imagery is shown in Figures 2.2, 2.3, and 2.4.
pictures 2.3 – Пример анализа съемки с БВС. Подсчет культурных растений (в штуках)
pictures 2.4 – Пример анализа съемки с БВС. Подсчет сорных растений (в процентах)
UAS-BASED OBSERVATION IN AGRICULTURE
Observation using unmanned aerial systems (UAS) can serve as a crucial tool for agronomists in assessing field conditions and crop yields. However, it is important to note that without proper data processing, agronomists may overlook critical details and indicators that could impact decision-making.
For example, without analyzing plant height, seeding density, soil composition, and other parameters, an agronomist might miss opportunities to optimize fertilization, crop protection, or irrigation strategies.
An example of UAS imagery analysis is presented in Figure 2.5.
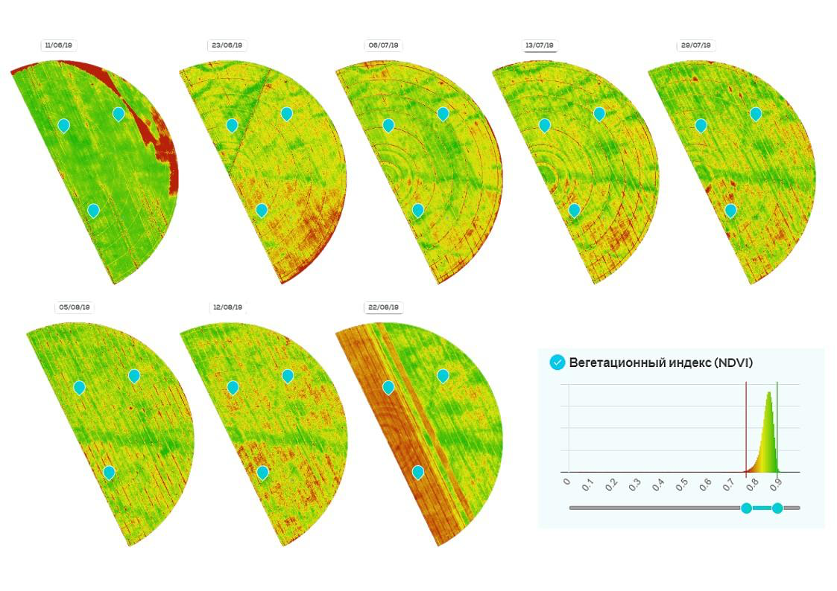
SOFTWARE USED FOR PROCESSING UAS DATA
The description of software begins with QGIS, a freely distributed open-source GIS platform. QGIS provides comprehensive documentation in Russian and has a dedicated Russian-speaking user and developer forum. This geographic information system (GIS) allows users to work with raster and vector data without conversion to a specific format. With its user-friendly graphical interface, QGIS enables the creation of maps and spatial data analysis. The system includes numerous functional and convenient tools for data visualization and processing.
QGIS allows seamless work with vector data, while raster data editing and importing require integration with GRASS GIS. The platform supports data processing and geospatial analysis, including distance and area calculations, geometric operations between datasets, and various spatial analyses.
QGIS is actively developed by an international community, with Russia represented by the NextGIS team. NextGIS QGIS is a fully functional desktop GIS used for data creation, editing, mapping, and analytics.
Another key software product featured in this review is Agisoft Metashape Professional, developed in Russia by Geoscan Group. Unlike QGIS, this is a proprietary (closed-source) software requiring a paid license. As of the time of writing, a standalone license for Russian customers is available on the Geoscan website for 315,000 RUB per computer.
Capabilities of Agisoft Metashape Professional:
• Processing images from RGB and multispectral cameras, including multi-camera systems.
• Transforming images into:
• Dense point clouds
• Textured polygonal models
• Georeferenced orthophoto maps
• Digital elevation/terrain models (DEM/DTM)
• Post-processing features:
• Removing shadows and texture distortions
• Calculating vegetation indices
• Generating prescription maps for agricultural applications
• Automatically classifying dense point clouds
The ability to export data to external post-processing software makes Agisoft Metashape Professional a universal photogrammetric tool.
Typically, QGIS (or similar GIS software) is used for storing, editing, analyzing, and visualizing digital projects (maps, plans, 3D models, etc.), while Metashape (or equivalent photogrammetry software) is used for converting raw UAS imagery into actionable geospatial products. Both types of software are essential for professional UAS data processing.
Cloud-Based Solutions for Storage and Post-Processing
For data storage and further processing, specialized industry solutions exist, such as the “Field History” cloud service and its “AssistAgro” module (by Geomir Group). These subscription-based services charge an annual fee based on the total field area uploaded into the system. As of the time of writing, the average cost is 60 RUB per hectare per year.
Key features include:
• Centralized storage of all collected imagery and orthophoto maps, linked to specific fields.
• AI-based image recognition, enabling:
• Automatic seedling counting for plant density assessment.
• Weed detection and quantification for evaluating field contamination.
These cloud solutions significantly enhance agricultural monitoring and decision-making by providing advanced data storage, analysis, and AI-powered insights.
2.1.1
DIGITAL MAPPING OF FARMLAND BOUNDARIES AND WINDBREAKS
Digital Mapping of Farmland Boundaries and Windbreaks is the process of automating and electronically documenting data on land plots used for agricultural activities. This ensures high accuracy in defining boundaries and securing land ownership rights.
Knowing the exact size of cultivated areas and their distance from each other is crucial for effective cost planning:
• Soil cultivation area using agricultural machinery and equipment – calculation of labor costs, fuel consumption for transportation and direct operation, and machinery depreciation.
• Sowing area – calculation of seed quantities, fertilizers, and plant protection products.
• Areas under different crops – cost estimation, yield forecasting, and preliminary profit calculations.
The digitization of agricultural land boundaries can be performed using satellite technologies, ground-based navigation and geodetic equipment, and other remote sensing methods, one of which is aerial photography using UAS. This allows for the creation of precise land mapping, which is particularly important for agricultural organizations, government agencies, and investors. When using UAS with high-resolution imaging (5 cm/pixel), horizontal errors (potential shifts in points on a plane) range from 5 to 10 cm, while vertical errors (for terrain assessment) are 10 to 15 cm. This ensures high accuracy in determining field boundaries, calculating areas within them, and constructing terrain maps (contour lines and water flow calculations).
Advantages of Digital Mapping of Farmland Boundaries and Windbreaks:
1. Simplified boundary determination – Digital technologies enable quick and precise boundary identification, reducing errors and costs.
2. Increased accuracy – Digital mapping ensures high precision in defining boundaries, which is essential for effective agricultural resource management.
3. Enhanced security – Digitized land boundaries help prevent disputes and conflicts related to boundary violations.
4. Improved monitoring – Digital boundary mapping facilitates the creation of land use monitoring systems, supporting environmentally sustainable projects.
Using unmanned aviation, every centimeter of a cadastral plot can be surveyed, allowing for the reliable identification of arable land, fallow fields, waterlogged areas, forest belts, roads, and other land categories, as illustrated in Figure 2.6.
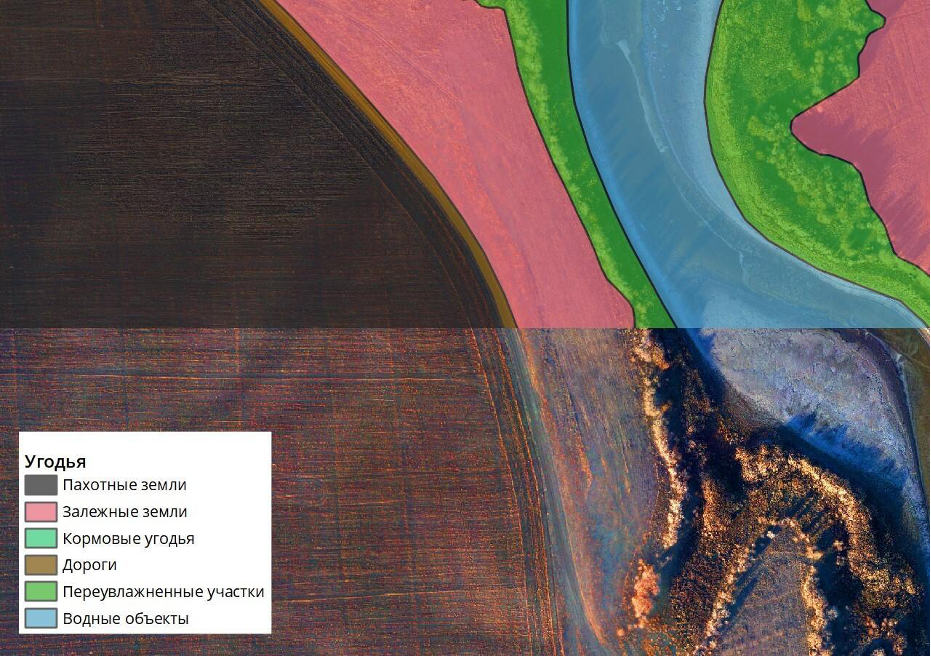
INVENTORY OF FOREST BELTS
Forest belts play a structural and functional role in the interconnections of agro-landscapes. Their effectiveness in enhancing field productivity and protecting soil from wind erosion has been proven through decades of observations. However, most forest belts were established about 70–75 years ago, after World War II, and the trees have now reached their maximum age. Over the decades, forest belts have expanded in width, reducing the total area of arable fields.
Due to this, some unscrupulous landowners or tenants engage in illegal logging of forest belts, which is environmentally unacceptable. At present, most forest belts require restoration. Before restoration, a preparatory stage is necessary, including the inventory of forest belts and the calculation of restoration costs. This also applies to forest belts along federal and regional highways.
The most effective way to inventory forest belts is through aerial surveys using UAS, followed by data processing. After identifying problematic areas in the forest belts, a dendrologist should be sent to conduct an on-site assessment and issue a report on the condition of the trees, allowing for an informed decision on removing deadwood.
It is evident that a comprehensive assessment of forest belt conditions using ground-based methods is highly time-consuming. With the help of UAS, data processing can be conducted quickly and efficiently using neural networks (artificial intelligence). In Russia, AI-based tree identification models have been successfully developed and applied since 2019, making forest belt inventory significantly faster and more accurate.
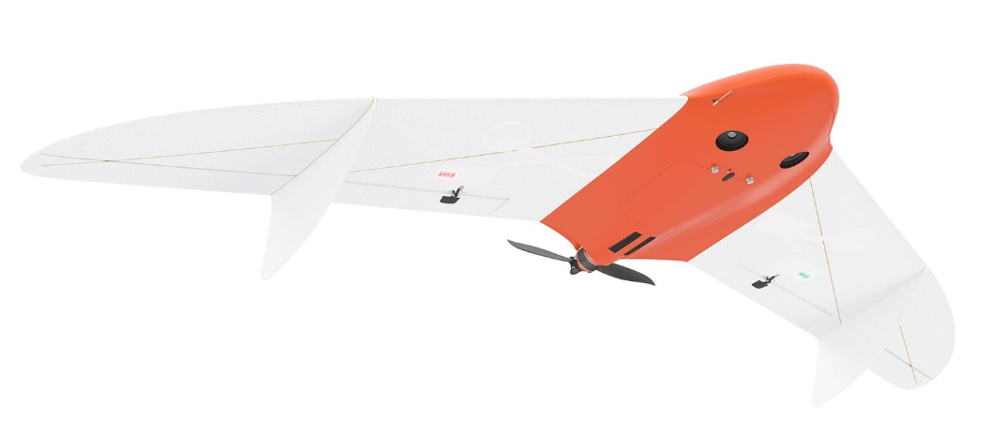
Workflow for Aerial Photography and Data Analysis
Part 1: Preparation for Aerial Photography
• Ordering cadastral extracts from Rosreestr
• Preparing aerial survey boundaries
• Determining the feasibility of aerial photography (checking for no-fly zones, coordinating flights in restricted areas or regions)
• Submitting a request to the General Staff of the Army for flight approval
• Requesting permission from the Military District Headquarters and the Regional FSB Office
Part 2: UAV Operation (After Obtaining Approvals)
• Traveling to the site
• Performing preparatory geodetic work
• Calibrating the multispectral camera
• Conducting aerial photography
• Sending collected data for review
Part 3: Office-Based Processing
• Photogrammetric processing with reflectance calibration of the multispectral camera
• Creating digital elevation models (DEM) and orthophotos
• Analyzing DEM
• Classifying cadastral plots
• Identifying unauthorized plowing
• Digitizing field boundaries
• Segmenting multispectral data
• Preparing recommendations for variable-rate application of fertilizers or pesticides
Legal and Weather Considerations for Aerial Photography
Legal Requirements
To legally conduct aerial photography, the operator must obtain:
• Operator Certificate (in accordance with FAP 494)
• License for handling state secrets
Weather Conditions for Optimal Results
The survey should be planned for a day with the best weather forecast. However, sudden weather changes during the survey can negatively impact the final results.
Factors That Can Affect Image Quality:
• Rain, snow, or strong wind (preferably under 5 m/s, but tolerable up to 10 m/s)
• Precipitation and fog should be avoided
• Multispectral imaging requires stable lighting, preferably clear or uniformly overcast weather
Optimal Timing for Surveys
• The best time frame depends on the survey objectives
• For agriculture, aerial surveys are typically conducted from April to September, when vegetation condition and growth stages can be assessed
• For terrain mapping, the survey should be conducted when the field is free from both snow and crops (bare soil conditions)
2.1.2
3D MAPPING, SLOPES, AND DRAINAGE ANALYSIS
What is 3D Mapping in Agriculture?
3D mapping in agriculture is the process of creating a three-dimensional model of a field or farm using specialized technologies and equipment. This technology enhances precision and efficiency in land management, resource allocation, and crop yield optimization.
3D maps allow for a volumetric visual analysis of terrain, helping to understand land configurations and features. The 3D terrain model of agricultural land provides a clear and realistic overview of the area without requiring a physical visit.
Advantages of 3D Mapping in Agriculture:
• Improved planning and management of crops and resources
• Increased precision in land cultivation
• Cost optimization for seeds, fertilizers, and pesticides
• More efficient irrigation and drainage system design
• Creation of digital field maps for further analysis and decision-making
• Identification of problematic field areas and corrective measures
Water Drainage Mapping
Water drainage maps in agriculture represent geographical layouts showing all water outflow systems, including rivers, streams, canals, lakes, and other bodies of water within farmland. These maps are essential for:
• Planning drainage systems
• Determining water flow direction and volume
• Assessing flood risk levels
• Choosing optimal soil treatment methods
Visualizing water drainage helps identify slope direction and detect areas prone to waterlogging. A sample water drainage map is shown in Figure 2.8.
Slope Mapping
Slope maps provide cartographic data for analyzing land elevation changes. They help identify fields or field sections with excessive slope angles. For such areas, it is recommended to:
• Adjust the direction of cultivation
• Utilize them for perennial grass crops
• Incorporate slope knowledge into crop rotation planning
A sample slope map is shown in Figure 2.9.
pictures 2.8 – Карта водостоков
pictures 2.9 – Карта уклонов
Technical requirements for creating high-quality 3D maps:
1. The spatial resolution of the images should be no higher than 10 cm/pixel, as the height error is up to 3 pixels. For such detailed shooting, high-resolution cameras and a relatively low flight altitude are required.
2. During shooting, the overlap of neighboring images should be at least 75-80%. Only with such overlap can reliable terrain and water flow maps of the required quality be created.
3. A powerful computer is needed for processing information and stitching the maps. The flight time takes minutes, while the calculation and map creation take hours.
4. The shooting should be conducted when there is no vegetation on the field (later, vegetation development can be monitored in 3D, which is good for yield forecasting).
3D terrain models can be built based on data obtained from the Geoscan 201 Agri-Geodesy UAV.
Additionally, equipment for airborne laser scanning can be used, for example, the DJI Matrice 350 UAV. However, in practice, laser scanning is rarely used in agriculture due to its high cost, and the higher accuracy of laser scanning is not an advantage over photogrammetric methods for obtaining dense point clouds in three-dimensional projection.
For processing the data obtained from UAVs, the photogrammetric tool Agisoft Metashape Professional can be used.
Timeframes and Cost of Work for a 10,000 ha Farm Example:
• Response to the request from the General Staff – 1 month.
• Response from the district headquarters and FSB – 1 month.
• Aerial photography execution – 1 working day (with a productivity of 5,000 ha per day per Geoscan 201 UAV, using a team with two UAVs).
• Control review – from 1 month.
• Digital Elevation Model (DEM) generation in software – 2 working days.
• Analytical work – 2 working days.
• Total cost: 500,000 RUB.
To perform aerial photography, an operator’s certificate (FAP 494) and a license for working with information classified as state secrets are required.
What can hinder obtaining a quality result:
• Rain, snow, or strong winds (preferably up to 5 m/s, and at most up to 10 m/s) on the day of the shooting.
• It is not recommended to conduct shooting during precipitation or fog.
For creating a terrain map, it is better to conduct the shoot when there is neither snow nor crops (vegetation cover) on the field.
2.1.3
AUTOMATED CROP CONDITION ASSESSMENT
To avoid errors when applying herbicides, increase yield, and monitor crop density, the “AssistAgro” module of the cloud service “Field History” (Geomir Group) can be used. This system allows field inspection of 100 hectares within 15 minutes using a small-sized multirotor drone. The plant recognition system helps identify which weeds are growing in specific phenophases and suggests the most effective herbicides to use. It also enables the calculation of crop plant density.
In such inspections, the fields are not scanned continuously to create an orthophoto plan, but rather at specific points from different sections of the field. The most effective method used is the “Chamomile” technique, where the field is scanned using “chamomiles” consisting of 6 or 8 images (Figure 2.10). The chamomiles are automatically placed evenly across the field. The number of chamomiles depends on the field size, usually: 3-4 chamomiles for up to 50 hectares, 6-8 for up to 100 hectares, and 1-2 for every additional 50 hectares. After forming the flight plan, the assignment is automatically sent to the drone via a mobile app.
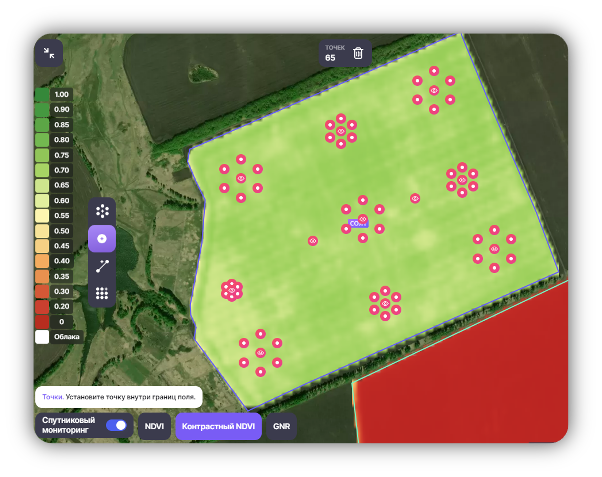
Using “AssistAgro,” farm managers can, regardless of their competence and the bias of the performer, receive information about the development of their crops: what the plant density of row crops is (which is very important, as their seeds are expensive and will become even more costly), what weeds are present in the field and in what quantity, and whether the plant protection products (PPP) were effective. The information obtained helps reduce the workload of agronomists, and in small farms, where there are no certified specialists, it aids in making timely and correct decisions. The system also predicts yield for the main agricultural crops, which helps determine the level of expenditure on plant protection. In high-yielding fields, the loss from weeds, diseases, and pests is greater, meaning more products should be applied, whereas in less productive fields, the opposite is true.
Weed recognition in crops of various plants.
озимая пшеница
подсолнечник
сахарная свекла
горох
рапс
соя
Evaluation of crop density.
сахарная свекла
соя
2.1.4
HARVEST INSPECTION
Harvest inspection or harvest control using UAVs is part of the general activities typically performed by the crop owner or security service to ensure the safety, timeliness, and correct delivery of the harvest. Generally, for this task, IoT sensors on harvesting machinery, information and telemetry collection from trucks, weighing, and surprise inspections are used.
Pre-harvest inspection is usually conducted for the following purposes:
1. Assessment of field readiness;
2. Possible scenarios for the use of desiccants (drying, accelerating ripening before technological harvesting);
3. Inventory of total area before harvest and yield forecast;
4. Monitoring of lodging (in case of lodging) – calculation of areas with lower-quality grain yield.
Forecasting yield before harvest also helps optimize machinery load, including logistics to warehouses or grain delivery points.
UAVs are used for monitoring fields (or orchards) during harvest, including cross-checking with telemetry data from equipment. Drones allow daily monitoring of harvested areas (comparison with inventory), as well as integration with logistics. Similar to video surveillance on highways, UAVs can read vehicle numbers, monitor drivers, and verify routes. Specific tasks for UAVs also include monitoring the geometric volume of open storage areas for harvested crops, allowing precise periodic scans to obtain data on changes in geometric parameters, for example, of sugar beet heaps, as shown in figure 2.10.
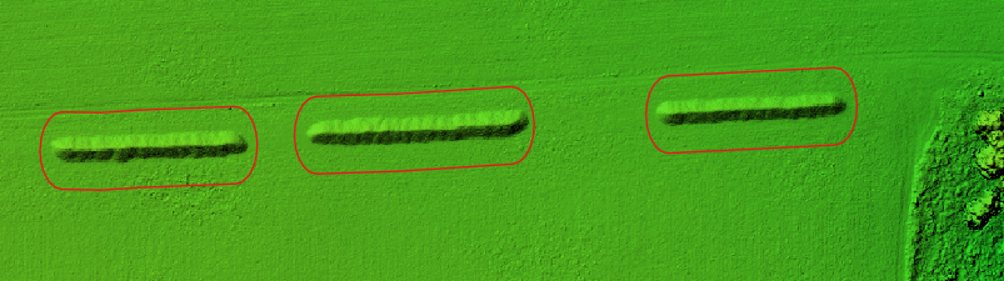
Aerial photography was conducted using the UAV “Geoscan 201 Agrogeodesy.”
For generating the digital elevation model, the software Agisoft Metashape Professional was used.
To digitize the heap boundaries and calculate their volume, QGis software tools were utilized.
Factors that reduce the quality of calculations:
• It is not recommended to conduct photography in the presence of precipitation or fog.
• Aerial photogrammetry should be performed during the snow-free period. Otherwise, fallen snow will distort the DEM and, accordingly, the accuracy of heap volume calculations.
• Additionally, the remote measurement method will allow the calculation of volume, but not weight, for which several additional parameters must be considered (e.g., root crop moisture, “density” of the heap, etc.).
Figure 2.11 illustrates a typical visualization of assessing the quality of agronomic operations.
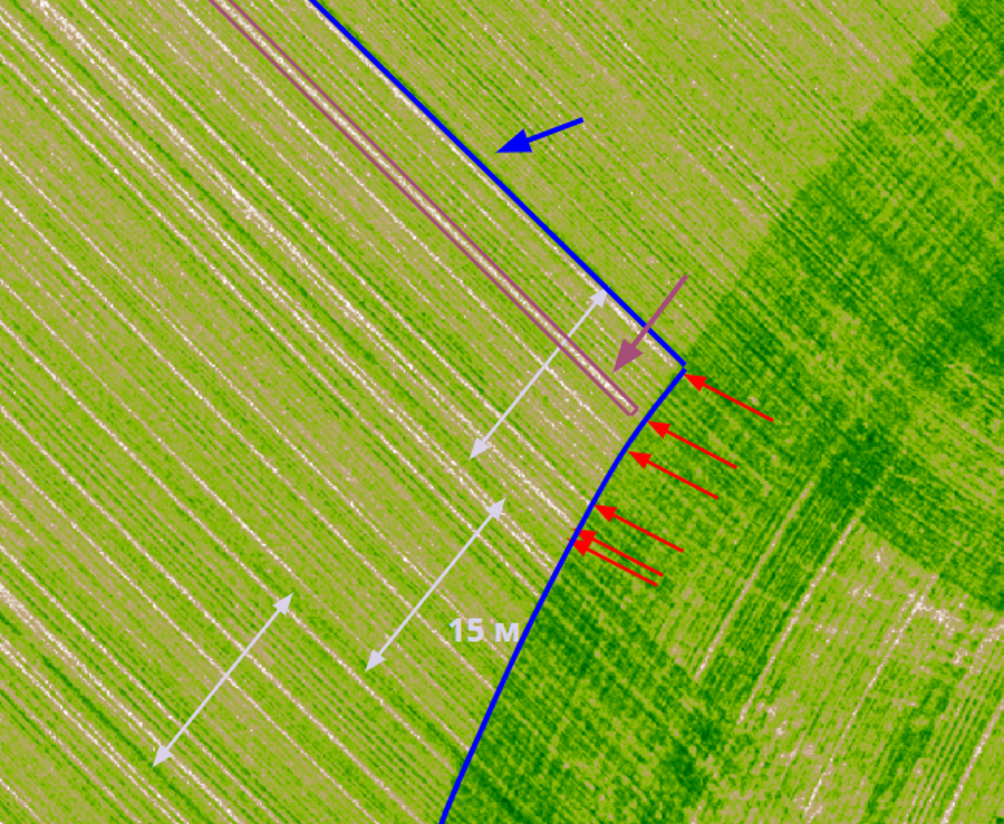
Aerial photography was conducted using the UAV “Geoscan 201 Geodesy.”
For generating the digital elevation model, the software Agisoft Metashape Professional was used.
To digitize the heap boundaries and calculate their volume, QGis software tools were utilized.
For the legal execution of aerial photography work, the contractor will require an operator certificate (FAP 494) and a license for handling information constituting state secrets.
Timeframes and Cost of Work for a 10,000 ha Farm Example:
• Response to the request from the General Staff – 1 month.
• Response from the district headquarters and FSB – 1 month.
• Aerial photography execution – 1 working day (with a productivity of 5,000 ha per day per Geoscan 201 UAV, using a team with two UAVs).
• Control review – from 1 month.
• Photomap generation – 2 working days.
• Analytical work to detect anomalies and assess the quality of agricultural operations – 5 working days.
• Total cost: 600,000 RUB.
Requirements for Aerial Photography Work:
To conduct aerial photography, an operator certificate (FAP 494) and a license for handling state secret information are required.
Factors That May Affect the Quality of Results:
• Rain, snow, or strong wind (preferably up to 5 m/s, with a maximum limit of 10 m/s) on the day of the survey.
• It is not recommended to conduct photography in the presence of precipitation or fog.
• For terrain mapping, it is best to perform the survey when there is neither snow nor vegetation on the field.
2.1.5
UAV-BASED AGRICULTURE SURVEILLANCE
Monitoring with UAVs, in contrast to previous scenarios, involves the operator (usually an agronomist) observing in real time the footage captured by the drone’s camera. The drone, typically a lightweight multicopter, is flown above the field (or orchard, vineyard, or melon patch). Essentially, this allows the operator to check what’s happening in the field in just a few minutes, without having to walk to the center or other parts of the field. By flying over the entire field, the operator can spot irregularities in crop color, height, or germination in the visible or multispectral spectrum. With manual control, the operator can also fly closer to anomalies and examine them in more detail.
For this task, DJI Mavic and Phantom drones are most commonly used. The application scenario does not require complex data processing, but the footage can be saved either by recording the screen or by storing individual photos, which can be revisited later if necessary.
This scenario typically does not require contractors and is often used by the farmer or in-house agronomist.
The cost of a DJI Mavic 3 drone is around 200,000 rubles, while a DJI Mavic 3 Multispectral with a multispectral camera costs between 500,000 and 800,000 rubles. An AgroScout drone from Albatros costs between 400,000 and 800,000 rubles for similar tasks.
Images showing the agronomist monitoring herbicide application on a field using the DJI Phantom4 RTK and the DJI Agras T30 are provided below in Figures 2.12, 2.13, and 2.14.
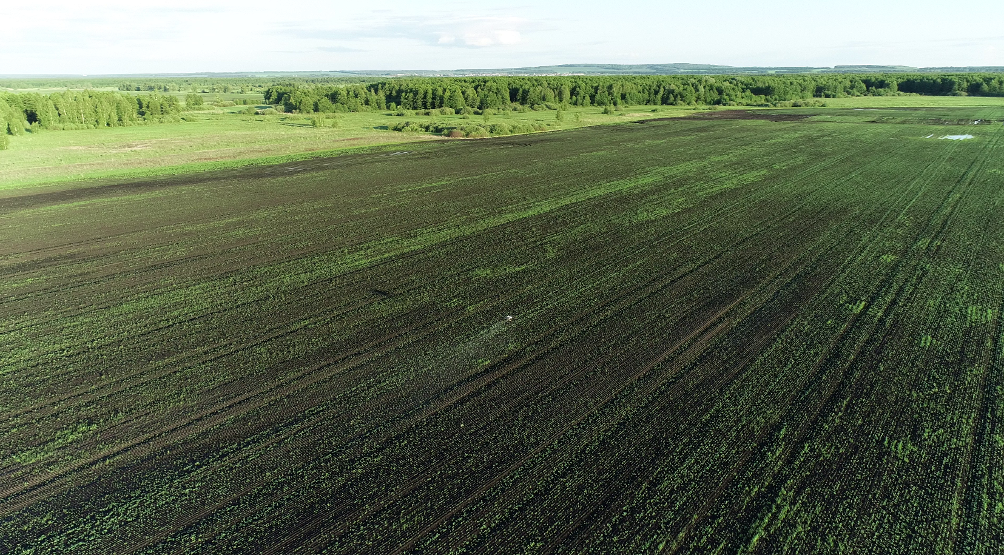
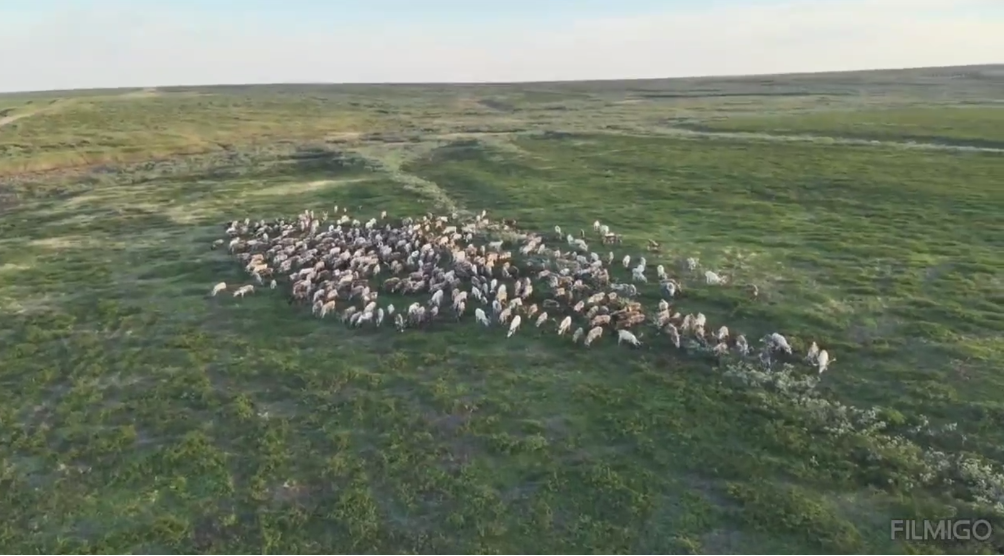
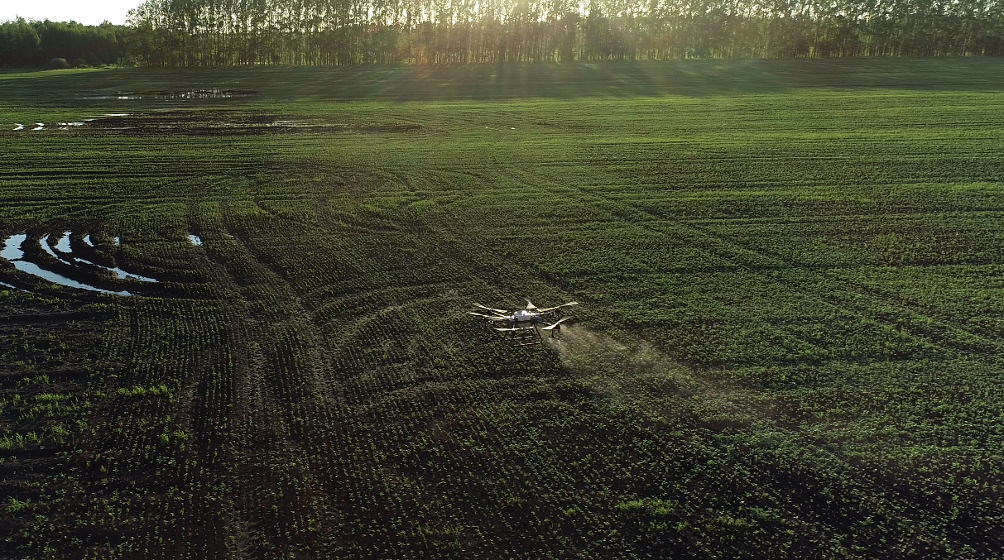
There is successful experience with the use of observer drones, including FPV drones as “flying herders.” However, for this to work, the drone operator must have a relatively high skill level in manual drone control.
The typical weather limitations include winds no stronger than 6 m/s (for some models, up to 10 m/s), no snow, and no heavy rain. In light rain, some drone models can still operate and provide quality footage when the camera is directed downwards (nadir view). It’s also important to consider that in cold weather, flight duration decreases due to the reduced capacity of the batteries. The typical flight time for observation is 20-30 minutes.
Observation using UAVs (Unmanned Aerial Vehicles) can be a crucial tool for agronomists in assessing the state of fields and crop yield. However, using the footage “by eye” without subsequent data processing has functional limitations. Without processing the data obtained through the UAV, the agronomist may miss important details that can affect decision-making. Therefore, this approach should be used rationally, combined with selective ground observation, measuring plant height, planting density, soil composition, and other parameters that are carried out without the UAV.
2.2
PERFORMING CORE AGRICULTURAL OPERATIONS USING UAVS
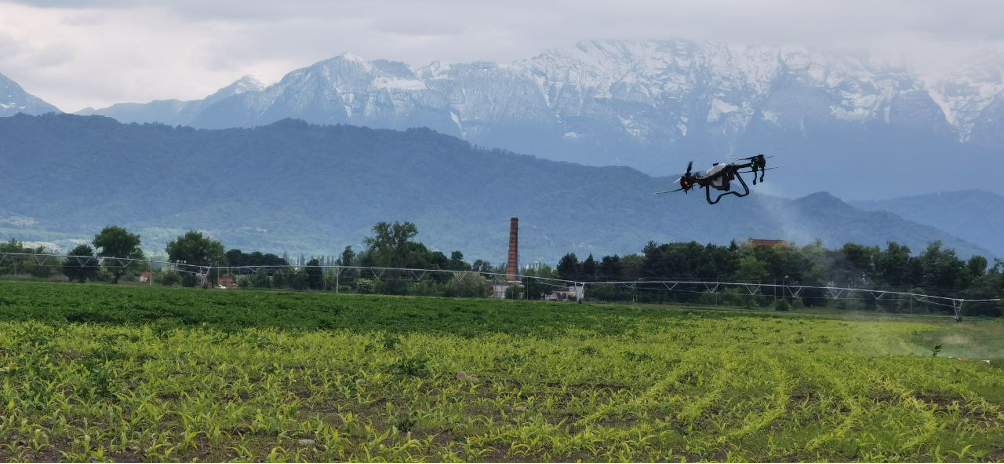
• Efficiency and mobility. For many farms that already use agricultural drones and have a fleet of modern ground equipment, the drone is now used as an “emergency service.” In these farms, drones are used for urgent unplanned treatments, as well as for correcting mistakes identified by the agronomist from the results of planned treatments with ground equipment or piloted aviation.
• Precision application. Thanks to precise positioning systems and the ability to perform treatments according to a pre-planned program in robotic mode, in most cases, it can be confidently said that the accuracy of application is higher, reducing the impact of human error.
• Reduction in the need for water delivery by 10 times. This is simple, as the agricultural drone allows the use of UMO technology, which will be discussed in more detail later, reducing the need for 200 liters of water per hectare to 20 liters (or even less) to achieve the same result. This is not suitable for all chemicals, although practice shows that the majority of registered pesticides do not lose their effectiveness when using UMO.
Agricultural operations are divided into the following types of operations:
1. Main technological operation – soil cultivation, seed sowing, plant care, harvesting, and post-harvest treatment. Soil cultivation and sowing include tasks such as: improving the physical properties of the soil, thereby creating favorable conditions for biological, physicochemical, and physical processes that enhance soil fertility; destroying the maximum number of weeds, pests, and plant pathogens; burying plant residues, mineral and organic fertilizers to a certain depth, thus creating a uniform plow layer that is favorable for the development of plant root systems; preparing a fine-structured, leveled seedbed and compacted seedbed, which ensure favorable conditions for seed placement and germination; sowing seeds into the compacted seedbed, evenly distributing them in terms of depth and field area. An example of agricultural drone use is shown in Figure 2.15.
2. Auxiliary operation – a set of actions that facilitate, improve, or ensure the execution of the main technological operation or change the position of the object being treated in space. Auxiliary operations can include transportation operations, weighing (measuring), quality control, and management operations.
The limitations of agricultural drones as tools for performing agricultural operations are usually related to a decrease in their productivity when the application rate (seeding or spraying) per hectare increases. However, this is the cost of operational efficiency and mobility, similar to the trade-off between wireless communication and data transfer via cable.
Therefore, agricultural drones cannot and should not completely replace traditional agricultural tools, but they have carved out their own niche in farms worldwide, reducing the use of both piloted aviation and ground equipment. Manual labor, still used on small fields (plots) and in household plots, can be completely replaced by agricultural drones.
Modern agro-technologies represent complexes of technological operations for managing production processes of agricultural crops in agrocenoses, aiming to achieve planned yield and product quality while ensuring ecological safety and economic efficiency. Agro-technologies are interconnected in a unified system for managing agro-landscapes through crop rotations, soil processing systems, fertilization, and plant protection, forming an integral part of adaptive-landscape farming systems.
These technologies have individual significance, primarily determined by the characteristics of the crop variety, as each type of variety (based on its purpose, intensity, and other parameters) corresponds to a specific system for managing the production process and the structural model of the agrocenosis.
Modern agro-technologies typically include agricultural use of unmanned aerial vehicles, satellite imaging of agro-industrial land assets, monitoring and analysis of crop growth using IoT sensors (climatic, microbiological, chemical, etc.), tracking growth phases and quality characteristics of crops using machine vision, use of artificial intelligence for analyzing crop growth intensity and making adjustments to cultivation technological maps, micro-meteorology, and machine-based management methods accounting for accurate weather forecasts, automated irrigation and computer-controlled watering systems, light and heat management in closed environments and greenhouses, intelligent software analysis for forecasting phytopathological diseases and pests, use of biotechnology, hydroponics, soil-less farming technologies, and the application of machine and deep learning for analyzing agricultural production efficiency.
The limitations in the use of agricultural drones also include the lack of widely available information on optimal input conditions for performing treatments in terms of “crop-pest-pesticide-volume of active ingredient per hectare-reduced rate of tank mix per hectare-drop size-height-speed.” Currently, this information is mainly shared among industry enthusiasts through Telegram chats, where they discuss the effects achieved under various treatment conditions. The authors of this review would like to see this review become one of the means for consolidating the accumulated knowledge of industry participants. They hope that the continuation of this review will involve regular activities to collect data on achieved effects, classification, independent verification, and wide dissemination of confirmed information.
In 1995, four categories of agricultural technologies were proposed based on the intensity factor [9]:
1. Extensive technologies: These technologies are oriented towards using the natural fertility of soils without the use of fertilizers and other chemicals, or with very limited use of them, and the application of tolerant varieties.
2. Normal technologies: These are technologies that involve the use of mineral fertilizers and pesticides at a minimal level that allows for the implementation of soil protection systems, maintaining a medium level of soil fertility, eliminating deficiencies in mineral nutrients at critical minimum levels, and providing satisfactory product quality. These technologies use flexible cereal varieties.
3. Intensive technologies: These technologies aim to achieve planned high yields of quality products in a system of continuous management of agricultural production processes, ensuring optimal mineral nutrition for plants and protection from diseases, pests, and lodging. Intensive technologies involve the use of intensive varieties and create conditions for the full realization of their biological potential.
4. High-intensity technologies: These are designed to achieve crop yields close to their biological potential with the desired product quality using the latest advancements in scientific and technological progress with minimal ecological risks. They focus on the use of precision equipment, modern chemicals, and information technologies. High-intensity or advanced technologies represent a qualitative leap in creating varieties, soil preparation, and enhancing technological operations for crop care. In high technologies, maximum integration of activities is achieved with consideration of their systemic interactions.
2.2.1
SPRAYING, DESICCATION, FERTILIZATION
Spraying is an effective method of using agrochemicals (primarily pesticides), which involves applying droplets of liquid pesticide solution, suspension, or emulsion to the surface that requires treatment. Various types of sprayers are used for this, including handheld, ground-based, and in our case—agricultural drones. [10]
Factors influencing the effectiveness of spraying:
1. Timeliness of treatment
2. Uniformity of application
3. Coverage degree
4. Dosage
5. Freshness (time from preparation) of the tank mixture
Considering the advantages of agricultural drones described in section 2.2, the effect of their use in a typical Russian farm is usually linked to the timeliness of the treatment and the freshness of the tank mixture. This is without considering the specifics of ultra-low volume spraying, which will be discussed in more detail below.
Spraying should be considered from two aspects:
1. Biological
2. Physicochemical
Biological Aspect
The biological aspect involves conducting spraying at optimal times. First, this is related to the toxicological appropriateness of applying pesticides to the sensitive stage or development phase of harmful organisms. Secondly, optimal timing is linked to the duration of the spraying process, which is limited by the development of the crop being protected. To achieve good biological results, the degree of coverage of the treated object is crucial. The degree of coverage is the ratio of the area of the surface covered by the pesticide solution to the total surface area of the object being treated. Based on a large experimental dataset, it has been established that for different types of pesticides, the degree of coverage should be at least:
• 0.5 – 1.0% for herbicides
• 2.0 – 3.0% for insecticides and fungicides
Physicochemical Aspect
The physicochemical aspect of spraying involves understanding the properties of the pesticides used, droplet size, degree of coverage of the treated surface, the rate of working fluid application, and the pH of the water. It is important to know at what air temperature spraying can be carried out to minimize the number of harmful organisms or avoid plant burns. It is also important to know the compatibility of pesticides when spraying with combined mixtures. For example, organophosphorus and pyrethroid insecticides decompose in an alkaline environment and lose their toxicity.
Thus, there are many factors, in addition to the instrument used for spraying (agricultural drone, self-propelled sprayer, or piloted aircraft), that determine the success of the operation. The professional operator—the agricultural drone pilot—must be knowledgeable about this information, as must the client (the client’s agronomist). Only in such a partnership of professionals can the maximum effect of the treatment be guaranteed without risk to the crop.
Median mass diameter of droplets.
Droplets are categorized into four groups based on this parameter:
• Aerosol – up to 50 µm
• Fine droplets – from 51 to 150 µm
• Medium droplets – from 151 to 300 µm
• Coarse droplets – over 300 µm
In spraying, there are several categories based on the volume of liquid applied per hectare:
• High-volume spraying – more than 300 l/ha
• Full-volume spraying – 200-300 l/ha
• Low-volume spraying (LV) – 75-200 l/ha
• Ultra-low-volume spraying (ULV) – up to 25 l/ha
The effective use of agrodrones in plant protection is closely tied to the emergence of ultra-low-volume spraying (ULV), along with the proven effectiveness of this technique with various pesticides and complex tank mixes. Therefore, ULV will be discussed in detail in this review, including its known advantages and disadvantages, which are often mistakenly attributed to the advantages and disadvantages of agrodrones using ULV. Many practitioners now associate ULV directly with agrodrones, which is not entirely correct, and we will attempt to distinguish between ULV, which can also be carried out by ground equipment and piloted aviation (which the authors have observed personally), and the use of agrodrones.
Advantages of ULV spraying:
• Higher biological activity of the pesticide, as it covers a larger surface area. With the use of agrodrones, due to the swirling air flow, the pesticide reaches the underside of the leaves.
• No runoff of agrochemicals into the soil. This is achieved by reducing the droplet size and the same air turbulence that keeps the pesticide on the plant cover. For comparison, during full-volume spraying, up to 30% of the pesticide is lost due to runoff into the soil.
• Reduced pesticide dosage in many cases, as the biological activity is higher and runoff is avoided.
• Fuel and labor cost savings due to fewer water deliveries.
• For low-water and arid regions, this also helps conserve water, which might not be available in sufficient quantities for full-volume treatments.
Disadvantages of ULV spraying:
• More susceptible to inversion effects. When meteorological anomalies occur, small droplets in ULV spraying increase the risk of drift and pesticide transfer. This is not due to the wind, which moves the droplets a fixed distance, but rather the ability of small droplets to remain suspended in the air for a long time and fall as dew, which is especially noticeable during low crop treatments or fallow land applications.
• Drift of the pesticide by the wind. This is a problem for inexperienced operators and creates difficulties when treating small plots. For larger fields (~100 ha), experienced BAS pilots can manage drift within acceptable limits without compromising the quality of the treatment.
• Evaporation of small droplets. At higher temperatures and air humidity, the “life span” of 200 µm droplets is 200 seconds, while for 50 µm droplets it is only 12.5 seconds. Therefore, in our country, spraying is more effective when conducted at night during hot summer periods.
• Higher water quality requirements. The optimal pH for most chemicals is around 6. Operators must closely monitor this parameter. Additionally, the longer the prepared working solution stands, the more it loses its effectiveness.
• Limited number of registered pesticides with ULV recommendations in Russia. This is a systemic issue, leading to two types of recommendations for water quantity in the tank mixture from pesticide manufacturers: official ones, based on previous tests when the pesticides were added to the catalog, and unofficial ones, where private information is shared about how a pesticide registered for full-volume application works under ULV conditions.
Insecticides are substances (or mixtures of substances) of chemical or biological origin intended to eliminate harmful insects. Among the various classifications of insecticides, the one of interest here is based on the method by which the toxin enters the insect’s body, which in turn determines the method of application:
• Contact insecticides cause poisoning of harmful insects through contact with any part of their body. They are primarily used against pests with piercing-sucking mouthparts. Contact insecticides are also effective against caterpillars of lepidopteran insects (butterflies and moths).
• Stomach insecticides poison insects with chewing mouthparts when the pesticide is ingested along with food and enters the digestive tract.
• Systemic insecticides are capable of penetrating the plant and moving through its vascular system, causing the death of pests that live inside leaves, stems, or roots. In addition, these substances can poison insects that feed on the plant.
• Fumigants are chemical agents that poison insects through the respiratory system.
Contact insecticides can and should be used with agricultural drones in the context of UAS-based plant protection technologies. Insecticides applied in the form of fine droplets at higher concentrations are significantly more toxic to pests and penetrate insect cuticles more quickly.
The biological efficacy of many active ingredients from the pyrethroid class has been proven when applied using agricultural drones, as well as that of combined formulations with neonicotinoids.
Which Formulations Are Most Suitable for UAV-Based Application (UAV Plant Protection Technology)?
• Microencapsulated Suspension (CS) – These pesticides are suspensions of active ingredients enclosed in a thin film-forming material shell. According to the catalogue of registered pesticides and agrochemicals, there are 10 CS-formulated pesticides, including both insecticides and herbicides. However, such formulations are significantly more expensive than traditional solutions.
• Water-Dispersible Granules (WG);
• Oil-Based Dispersions (OD).
There is no unanimous opinion on which formulation type is the most effective for UAV-based application. However, it is important to understand that the ultimate suitability is determined by the density of the solution—the closer it is to the density of water, the better the performance. Additionally, the volatility of the active ingredient must be taken into account.
Fungicide – a substance of chemical or biological origin intended for the control of plant diseases.
Based on their mode of action, fungicides can be classified as:
• Preventive (protective);
• Curative (therapeutic, eradicative);
• Immunizing.
For the purposes of UAV-based agricultural applications, there is practical experience with the use of the following fungicides (by active ingredients):
• Propiconazole
• Cyproconazole
• Azoxystrobin
• Copper compounds (on fruit crops before bud break)
One of the essential skills in performing spraying operations is the preparation of a tank mix, which becomes especially important in UAV-based spraying (UASS) due to the high concentration of active ingredients. Tank mixes are a valuable means of enhancing both the biological and economic efficiency of plant protection products. They allow for the simultaneous control of weeds, pests, and diseases. This approach not only helps slow down the adaptation of harmful organisms to commonly used pesticides, but also reduces the overall pesticide load on treated areas, improves labor productivity, saves fuel and lubricants, decreases mechanical damage to crops, lowers the cost of agrochemical applications, and helps preserve soil structure and humus content.
For example, using a combination of small doses of two or more pesticides may provide the same biological efficacy and duration of protection as a large dose of a more toxic single-agent product.
There are two main types of mixtures:
• Factory-formulated mixtures (combined preparations) manufactured by chemical companies;
• Tank mixes prepared immediately before spraying.
The use of pesticides in tank mixes is now widespread in crop protection practices, both in Russia and internationally.
Tank mixes may include pesticides of the same type (insecticides, fungicides, or herbicides). Such combinations are used to broaden the spectrum of activity and increase effectiveness against specific harmful organisms. Additionally, tank mixes may include pesticides with different functions, enabling simultaneous control of multiple types of pests and diseases.
Herbicide – a chemical plant protection product used to control unwanted vegetation, primarily herbaceous weeds.
Depending on the purpose of application, herbicidal products are classified as follows:
• Herbicides – used to eliminate weedy plant species;
• Arboricides – substances intended to suppress shrubs and tree vegetation;
• Algicides – agents effective against aquatic plants.
Some formulations may have a combined effect in two or more of these categories.
Depending on their spectrum of activity, herbicides can either eliminate all plant species or selectively target specific ones. Based on this, they are divided into two main groups:
1. Non-selective herbicides: These destroy any vegetation they come into contact with and are commonly used in the treatment of sports grounds, irrigation canals, roadways, and other non-agricultural areas.
2. Selective herbicides: These selectively damage certain plants and are applied during the cultivation of agricultural crops. Selective herbicides can be further divided according to their degree of selectivity:
• Broad-spectrum selective herbicides (e.g., triazine derivatives used in corn fields suppress a wide range of both dicotyledonous and monocotyledonous weeds);
• Narrow-spectrum selective herbicides, which affect only specific weed types.
For use with agricultural drones, practical experience has shown the effectiveness of herbicides containing the following active ingredients: Glyphosate, Dicamba, Prometryn, Sulfonylurea, and Mesotrione.
Extreme caution is advised when applying 2,4-D and Bentazone—attention must be paid to the absence of temperature inversion risks during application. Spraying must not be carried out under conditions that could lead to fog formation.
It is also important to note that Triazines, Thifensulfuron-methyl, and Clethodim may demonstrate reduced efficacy when applied via UAV-based spraying (UASS).
Practical experience and scientific research indicate that the use of pesticides in tank mixtures is advisable only when the timing of application for each component coincides and the physical and chemical compatibility of the components is ensured.
Choosing the optimal timing for the application of tank mixtures is a critical factor in implementing plant protection measures. In practice, incorrectly selected spraying times are often the primary cause of failure. This factor becomes particularly important when the mixture includes products with differing application windows.
When using pesticides in tank mixtures, it is necessary to consider not only the physical and chemical properties and interactions of the active ingredients, but also those of the formulation components—such as surfactants, fillers, stabilizers, solvents, and specific additives.
During the preparation of tank mixtures under field conditions, changes in the physical and chemical properties of the components may occur, potentially increasing the toxicity to cultivated plants. To avoid such negative effects, it is essential to follow basic mixing guidelines when combining plant protection products.
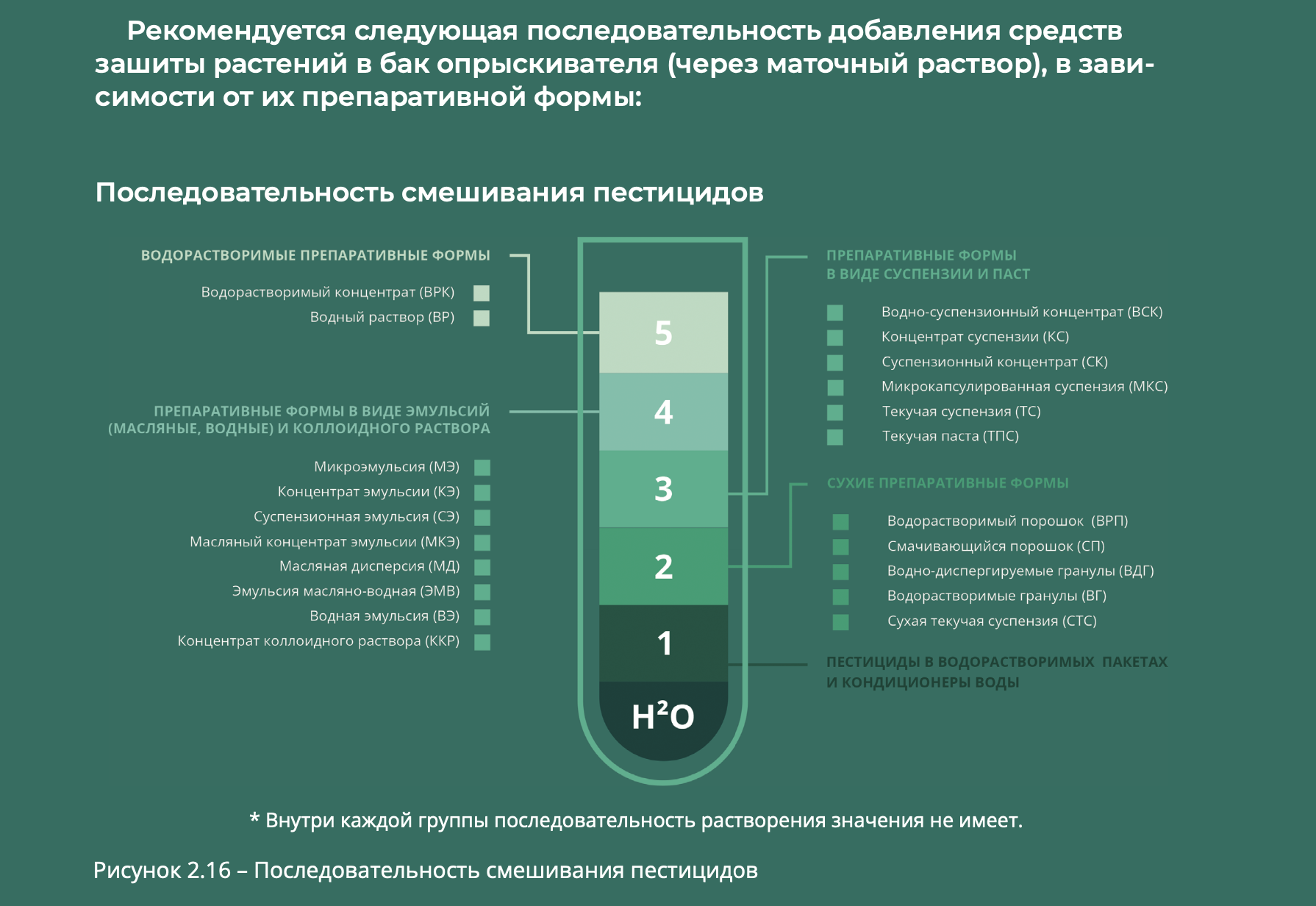
Variable-rate application and partial field treatment.
Given the robotic nature of agrodrone operations, performing partial or selective field treatment—such as perimeter spraying or targeting specific weed-infested patches—poses no difficulty using the standard functionalities of any modern agrodrone’s software.
Figure 2.17 shows zones where weed infestation exceeds the economic threshold of harmfulness. The total area of such zones does not exceed 10% of the entire field. By designating these zones in the flight plan as targets for herbicide application, it is possible to achieve significant savings on pesticide costs.
Desiccation refers to the spraying of crops with chemicals that promote the dehydration of plant tissues (rapid drying of foliage). This operation is typically performed 5–15 days prior to mechanical harvesting, with the main objective of facilitating combine harvester operations. Depending on crop development, desiccation can be carried out across the entire field or selectively in certain areas. When glyphosate is used as a desiccant, it also helps eliminate late-emerging weed overgrowth, which can otherwise complicate harvesting.
The prevailing market rate for drone-based desiccation is approximately 1,000–1,500 rubles per hectare (1,500 for single-field jobs, 1,000 per hectare for orders exceeding 20,000 hectares). The direct cost for a farmer performing the operation independently is around 500 rubles per hectare. The cost difference is mainly due to transportation expenses and the fee of an external drone operator.
Compared to ground-based desiccation, drone application is fully justified by eliminating crop losses from trampling or damage caused by the booms of ground sprayers—especially important when the crop is near maturity.
All modern desiccants perform well when applied using ultra-low volume (ULV) technology. Their effectiveness is so high that the application rate can be reduced by 25–50% when used with agricultural drones.
An unconventional method is senication using a 30% solution of ammonium nitrate combined with a 0.01% solution of amine salt herbicide, applied at a working fluid rate of 12 liters per hectare. This approach significantly reduces crop drying costs and improves the quality of soybean, corn, sunflower, and grain yields.
Senication is an agronomic technique aimed at increasing the productivity of cereal crops. It enhances the translocation of assimilates from leaves to grain, resulting in increased kernel weight, improved grain quality, and accelerated maturation. This method is particularly useful in cases of uneven ripening, delayed harvest, or productivity loss of up to 40%. Unlike desiccation, senication does not dry out the crops; instead, it promotes grain filling by stimulating phloem flow, thereby transferring photosynthetic products to the grain. As a result, gluten content, thousand-kernel weight, and other quality indicators improve. Furthermore, senication can be performed at lower temperatures, making it effective regardless of weather conditions.
Defoliation is the natural or artificial process of leaf fall caused by environmental stressors or induced by chemical agents known as defoliants. In China, thousands of agricultural drones are used for the defoliation of cotton.
Pod sealing is employed to prevent yield loss due to pod shattering. This is done through aerial spraying of formulations containing elastic substances. Upon contact, the spray droplets spread and coalesce on the pod surface, forming a continuous elastic film. There is proven success in applying pod sealants to rapeseed using agricultural drones.
Spraying trees typically requires specialized mechanized equipment capable of delivering insecticide as an aerosol or a high-pressure jet to reach the upper tree canopies. However, such technology proves economically inefficient when dealing with isolated pest outbreaks. Moving the equipment to the treatment site, the large capacity of the sprayer tank (designed for treating hectares of forest stands), and other related factors lead to unjustified expenses.
For localized infestations, drone-based spraying is an ideal solution. This method allows for precise, targeted application of insecticides directly to affected areas, as illustrated in Figure 2.18. Figure 2.19 shows an outbreak of the American white moth caterpillar (Hyphantria cunea) on a box elder (Acer negundo) in a shelterbelt.
pictures 2.18 – Опрыскивание лесополосы от вредителей
pictures 2.19 – Очаг гусениц американской белой бабочки на деревьях клена ясенелистного в лесополосе на юге РФ
2.2.2
FERTILIZER APPLICATION
Agricultural drones are capable of applying both liquid fertilizers (foliar feeding) and granular fertilizers. Foliar feeding (as well as pesticide application) is performed on the surface. The absorption of nutrients occurs through their uptake by the leaf surface. This method is considered the most effective and economical for applying micronutrients.
Foliar feeding is carried out during the growing season upon visual identification of micronutrient deficiencies in plants. This application method allows for timely correction of micronutrient deficiencies while simultaneously preventing the negative consequences of micronutrient application to the soil.
Foliar feeding can be performed using BAS (Precision Agriculture Systems). This is particularly advantageous when it is necessary to apply fertilizers in differentiated doses (as part of the precision farming concept). Initially, BAS is used to determine vegetation indices, based on which a fertilization algorithm for the crops is developed. The fertilizer is then applied to the precise location in the required dose using a drone. This foliar fertilization or plant protection treatment technology can also be successfully utilized in nurseries of woody plants, vineyards, and industrial orchards.
Thus, to carry out the application of plant protection agents and fertilizers in differentiated doses, three stages are required:
1. Survey using BAS (fieldwork);
2. Data processing, analysis, and creation of an application map (office work);
3. Application of pesticides or agrochemicals using an agricultural drone (fieldwork).
Important Considerations When Using Agricultural Drones:
• Chelated forms of micronutrients do not exhibit harmful effects on plants, even when the working solution is applied at reduced rates.
• Combined foliar fertilizers: Many manufacturers claim that effective treatment can be achieved at an application rate of 5 liters per hectare. These formulations typically contain not only micronutrients but also essential macronutrients such as nitrogen, phosphorus, and potassium.
• The growth regulator trinexapac-ethyl is effectively used in drone-based applications for crops grown under precision agriculture systems (УМО).
• A question remains regarding urea and the use of a 40% urea solution as a solvent for pesticides in tank mixes. This issue necessitates further research and experimentation.
Macronutrients (Nitrogen, Phosphorus, Potassium)
Macronutrients such as nitrogen, phosphorus, and potassium are typically applied to the soil prior to sowing as starter fertilizers. Numerous farms have reported successful experience in applying NPK (nitrogen + phosphorus + potassium) using agricultural drones equipped with standard onboard spreaders, at application rates of 120 kilograms per hectare.
It is important to note that the cost of drone-based application at a rate of 100 kilograms per hectare amounts to approximately 3,000 rubles per hectare. Given this expense, the economic efficiency of using agricultural drones for application rates of 100 kilograms or more can only be justified under specific conditions—namely, when ground-based equipment cannot access the field, or when no functional ground-based machinery is available.
Note: Nitrogen, as one of the macronutrients, may also be applied in the form of supplementary feedings. Accordingly, its application via drones is feasible in fractional doses several times throughout the growing season. This approach allows for the avoidance of an excessive single-time “shock” load on the environment, thereby promoting more sustainable agricultural practices.
2.2.3
AERIAL SEEDING
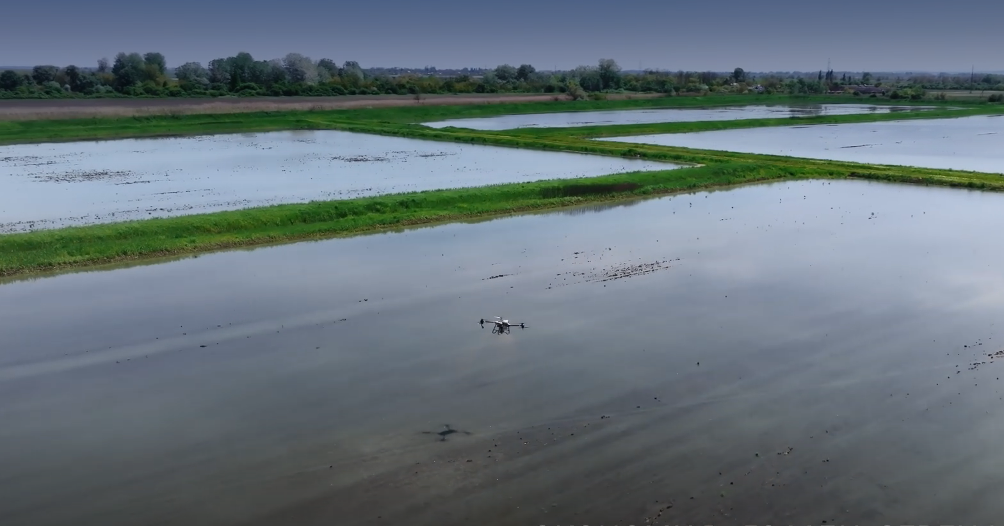
In Russia, there has been successful experience not only in the aerial seeding of rice, but also of rapeseed, mustard, and various annual and perennial grasses.
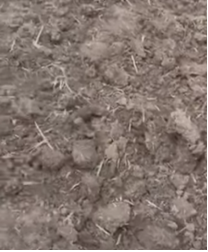
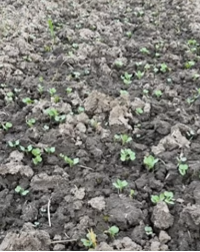
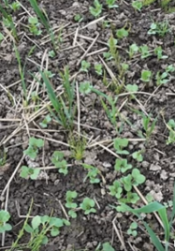
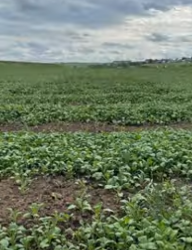
In addition to surface seeding and seeding into water-filled paddies, there is also a practice of seeding with the use of agricultural drones followed by mechanical incorporation of the seeds into the soil. At present, this method is most commonly employed as a necessary, reactive measure—typically when ground-based seeders are unable to perform the operation for various reasons—thus serving as an “emergency response” rather than a primary tool.
Nevertheless, it cannot be ruled out that, over time, this method of seeding may become more widespread for certain crops, as agricultural technologies continue to evolve and adapt to new methods of operation—including the integration of agricultural drones.
2.2.4
APPLICATION OF ENTOMOPHAGES
In recent years, Russian agriculture has faced a range of new challenges, including the growing threat posed by insect pests that cause substantial damage to crops. One promising—albeit still underdeveloped—approach to combating these pests is the use of entomophages: predatory insects that feed on harmful species and their larvae without causing harm to agricultural crops. This biological method of pest control is considered more environmentally friendly and natural compared to conventional chemical insecticides.
Entomophages, often referred to as nature’s plant defenders, represent a diverse group of beneficial insects. Among the most prominent are Trichogramma, Habrobracon, and Chrysopa (green lacewing), each playing a vital role in the biological protection of plants.
Trichogramma is one of the most widely used entomophages. It lays its eggs inside the eggs of pest insects, effectively destroying them at the embryonic stage. A single female Trichogramma can parasitize 20 to 40 pest eggs, with a flight radius of up to three meters. During one growing season, Trichogramma may produce five to six generations, enabling it to maintain consistent control over pest populations throughout the season.
Habrobracon, on the other hand, targets the larvae of pests such as the European corn borer and the cotton bollworm. It paralyzes the caterpillars by injecting a toxin through its ovipositor, causing them to cease feeding and growing, thereby reducing their harmful impact. The biological efficacy of Habrobracon reaches up to 82% in cornfields and 88% in sunflower fields, making it a powerful tool in pest management.
The green lacewing (Chrysopa) is another highly effective entomophagous insect, feeding voraciously on caterpillars, aphids, thrips, and other small pests. Its larvae are particularly efficient, consuming hundreds of harmful insects during their short life cycle, making them indispensable allies in pest control strategies.
Technology of Entomophage Application via Drones
Since 2017, Russia has been actively developing technologies for the aerial application of entomophages using unmanned aerial systems (UAS)—commonly known as drones. The deployment of drones enables the swift and even distribution of beneficial insects across large agricultural areas, significantly enhancing the overall effectiveness of biological pest control.
The adaptation of drone-based dispersal mechanisms to specific agronomic tasks is opening new horizons for the efficient introduction of beneficial insects, ensuring both flexibility and high productivity in agricultural operations. Such innovations are particularly crucial in the context of climate change and resource scarcity, where resilient and sustainable solutions are increasingly in demand.
The process of crop protection through entomophage release using UAS represents a modern, high-tech, and effective strategy for pest management. At the heart of this system are drone platforms such as the DJI Matrice 100 (M100) and DJI Matrice 600 (M600), which ensure precise and uniform dispersal of entomophages over cultivated fields.
However, the current landscape is marked by a shortage of spare parts and consumables for imported equipment. In response, efforts are underway to develop a universal domestic drone platform, capable of replacing existing foreign-made models. Its principal advantage lies in its adaptability—allowing for integration with various tasks and dispersal mechanisms, thereby ensuring greater operational flexibility.
To achieve effective application of entomophages, a range of specially designed dispersal units is employed. For instance, devices used for Habrobracon and Chrysopa are available in two variants, differing in their kinematic structures and control systems. This allows operators to select the most suitable tool for the task at hand, further enhancing the efficiency and precision of biological pest control using drones.
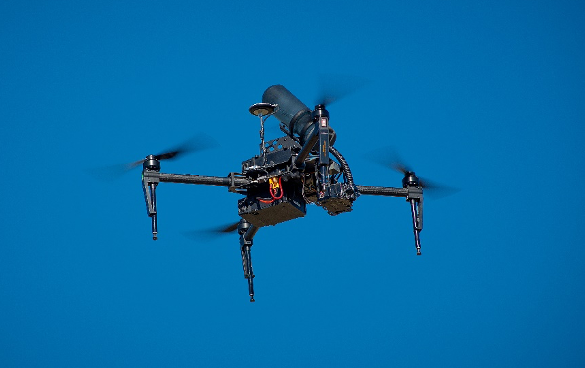
The second version of the dispersal unit features a more complex architecture, with a controller based on the STM32 chip integrated with the flight controller of the M600 platform. This integration allows for pre-programming of entomophage release points and enhances treatment in areas with pest concentrations. Additionally, the release can be manually controlled in the event of GNSS signal loss, making the system more reliable.
A key component of the second version is the charging and calibration station, which automatically charges the disperser with cassettes containing entomophages. These cassettes consist of corrugated cardboard sheets, onto which entomophages, such as Gabrbrocon (in larval form) or Chrysopa (in egg form), are attached.
In addition to these systems, new dispersers are being developed for other entomophages, such as Trichoderma. This system will be capable of generating a dust cloud for the even distribution of beneficial microorganisms, further expanding the possibilities for biological crop protection.
The development of UAVs (Unmanned Aerial Vehicles) and the improvement of entomophage application technologies represent an important step toward sustainable agriculture, where the impact of chemical substances on the environment and agricultural products is minimized.
The use of drones for the application of entomophages in agriculture opens new opportunities for effective pest control. The key advantages of this technology include:
1. Accuracy and uniformity of distribution: Drones ensure precise application of entomophages, which is especially important for dealing with pests that breed unevenly. This allows for effective coverage of large areas and hard-to-reach sections of fields.
2. Reduced treatment costs: The automation of the process through drones significantly reduces labor costs and the time required for field treatment. This makes the method economically viable and accessible for widespread use.
3. Speed of application and round-the-clock operation: Drones can quickly cover large areas, greatly increasing the efficiency of protective measures. Additionally, they can operate at night, which is particularly useful for plant protection when daytime treatment might be difficult or undesirable.
The comprehensive service for plant protection using entomophages with drones is a multi-stage process that involves the work of various specialists and the use of advanced technologies. The main stages of providing this service are as follows:
1. Field Study and Its Features: The first stage involves the agricultural service team visiting the site. Specialists conduct an inspection of the crops and analyze the geographical location of the field, its features, and condition. It is crucial to assess the access routes for the pilot service, evaluate the satellite navigation signal strength necessary for the flight task, and install pheromone traps, such as those for the cotton bollworm, to monitor pest activity.
2. Initial Monitoring and Forecasting: Over 5-10 days, a follow-up inspection of the field is carried out, during which specialists assess the state of the crops and the pest population. Based on the pest flight forecast and the current field situation, the economic threshold of pest damage (ET) is determined, and the timing for the release of entomophages is scheduled. If protection is needed, the most effective type of entomophages is selected, and a release schedule is developed.
3. Initial Release of Entomophages: Based on the results of the monitoring, the pilot service promptly and timely releases the entomophages on the field using drones. Unique schemes and algorithms are applied for each specific field, ensuring maximum efficiency of the treatment. Different types of entomophages, such as Gabrbrocon and Chrysopa, use appropriate dispersers.
4. Effectiveness Control and Trap Replacement: After 5-10 days, a follow-up inspection of the field is carried out to assess the effectiveness of the entomophages applied. If necessary, specialists replace the pheromone traps and determine the timing for the next bioagent application.
5. Secondary Release of Entomophages: A secondary release of bioagents is carried out to maintain a stable level of crop protection and minimize losses from pest insects.
6. Final Control and Effectiveness Assessment: The final stage includes an inspection of the field 5-10 days after the secondary release of entomophages. An analysis of the effectiveness of biological protection is conducted.
This multi-stage process allows for the effective protection of agricultural crops from pests, minimizing the use of chemical pesticides and ensuring the ecological purity of the products.
In Table 2.5, a comparison of three different methods of pest control for agricultural crops is presented: the use of self-propelled machinery, aviation (using the Bekas aircraft), and the innovative approach with the application of entomophages using drones. Each of these methods has its own characteristics, advantages, and disadvantages, which influence the choice of agronomists and farmers depending on the specific conditions.
Self-propelled machinery generally allows for the processing of relatively large land areas but requires additional costs for maintenance, such as fuel and servicing. Aviation, on the other hand, offers the ability to treat hard-to-reach areas, but is limited in terms of area and may be less effective in impacting pests. The use of drones with entomophages allows for a significant increase in the area treated and guarantees high pest control efficiency. This table presents the key parameters and results of each method, which allows for a visual evaluation of their effectiveness and economic feasibility.
Despite the obvious advantages, the technology of applying entomophages using drones is still in the active implementation and research phase. One of the challenges is the limited scientific data supporting the effectiveness of this method. Nevertheless, the results of already conducted experiments and practical applications show that the use of entomophages in combination with advanced technologies can significantly improve the efficiency of crop protection.
Furthermore, an important aspect remains the issue of the availability and production of entomophages. Trichogramma is already widely available on the market, while the production of Gabrus bracon and lacewing is still insufficiently developed. However, the further development of this area promises to be an important step towards more sustainable and environmentally friendly agriculture.
Рис. 2.2.5. Иллюстрация внесения энтомофагов (трихограммы) с применением БВС
Рис. 2.2.6. Иллюстрация внесения энтомофагов (златоглазки) с применением БВС
The use of entomophages with drones represents an innovative and environmentally friendly method of crop protection. The development of these technologies and their widespread implementation could become an important element of the sustainable agriculture strategy, reducing dependence on chemical insecticides and promoting the preservation of biodiversity.
2.2.5
HARVESTING
Harvesting crops is still considered an exotic application of drones. However, it is not something impossible. While there are no economically justified examples of drone use during harvest in Russia, there are several examples of how this could be applied:
The Israeli startup Tevel Aerobotics Technologies has developed autonomous flying drones that take off from a base station, pick only ripe fruits from trees, and gently lower them for collection. Since they are not humans, Tevel’s robot harvesters can work around the clock, seven days a week, during the harvest season. They never get tired, they never need coffee breaks or restroom visits, and they do not plan vacations. TEVEL AEROBOTICS TECHNOLOGIES [16]
HMC Farms® has partnered with Tevel Aerobotics Technologies for a pilot launch of their crop harvesting system using flying autonomous robots, as shown in Figure 2.20. A representative from HMC states that this summer, the peach, nectarine, and plum harvest was successfully completed with drones: “This project is still in its early stages, but the future potential is very impressive.”
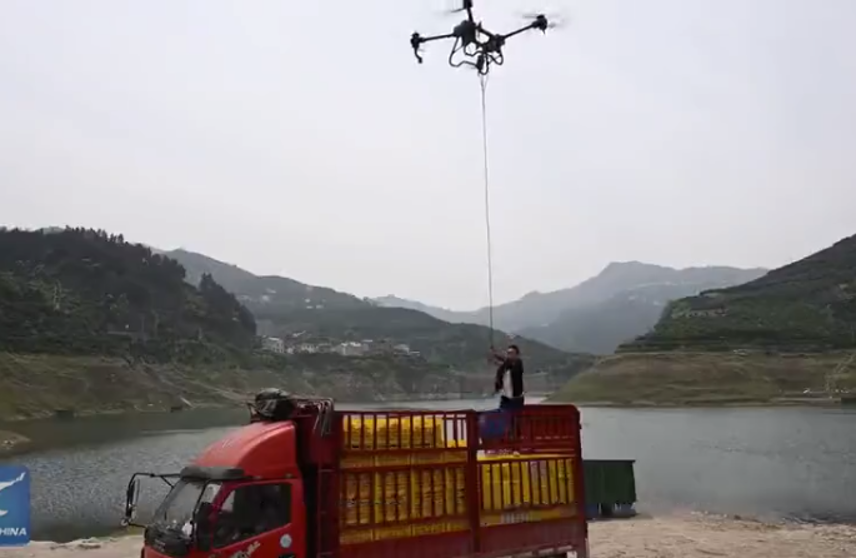
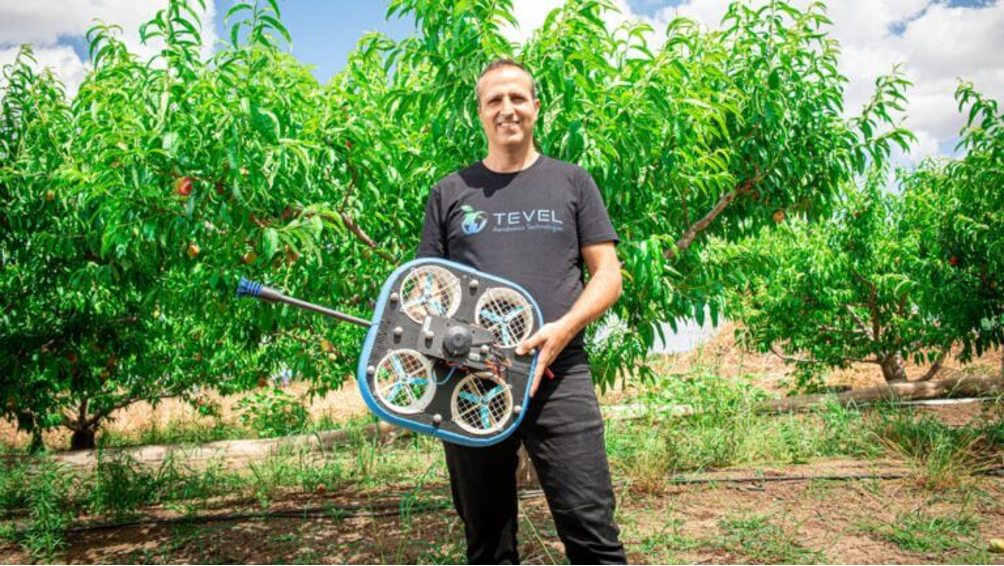
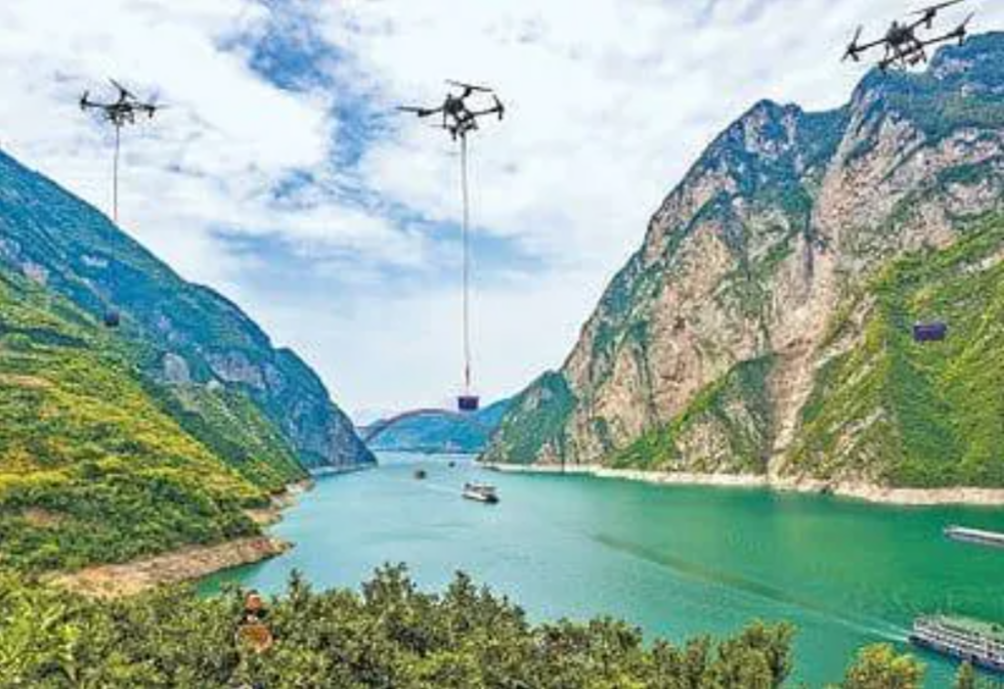
Drones transport oranges in an orchard by the Yangtze River in Zigui County, Hubei Province, central China. Farmers manually harvest the oranges, fill special baskets, and then a cargo drone arrives at the designated point with a rope. A person on the ground attaches the basket to the rope, and the drone carries it to the road, where it is transferred to road transport. The weight that the drone lifts is around 50 kg.
The oranges in this province grow in mountainous terrain, and previously, a person was used to collect the fruit. In a day, they could carry down 50 kg from the mountain. With further automation, single-track paths for mechanical carts were established, but the capital costs for such paths were very high, making their use unprofitable.
In recent years, the promotion of agricultural drones led to the creation of a drone service company in Zigui County, which revolutionized the transportation of oranges. This year, during the orange harvest season, around 200 drones were involved in the transportation process.
“The demand for transporting oranges with drones has increased, and we have trained more than 400 pilots,” said Liu Huide, the head of the agricultural service company in Zigui.
“Each drone is equipped with three rechargeable batteries, allowing it to operate continuously. Each flight covers a radius of about 300 meters, and the agricultural drone can transport 10 tons of oranges per day,” said Liu Dehui. He added that using drones to transport oranges is fast and economical, with the average transportation cost being only 3.7 rubles per kilogram of oranges.